Welded Plate Heat Exchangers
What is a Welded Plate Heat Exchangers
Welded Plate Heat Exchangers are a type of heat exchanger used in industrial process applications, often for semi-fouling or viscous media or when temperature or pressure is higher than technically possible for Gasketed Plate types. Most often corrugated plates are used and these are welded together creating a multi-channel passage for the media. The media, separated by the plates, normally flow in cross flow / counter current (when more than one pass is used).
Below description of the following types of Welded Plate Heat Exchangers that we can provide:
- Welded Plate Heat Exchangers with Corrugated Plates mounted in a frame with bolted side panels forming a block shape – GreanBoxTM – Model S
- Fully Welded Plate Heat Exchangers with Corrugated Plates mounted in a fully welded frame with semi-shell side panels forming a cylindrical block shape – GreanBoxTM – Model W
- Welded Plate Heat Exchangers with Studded Plates mounted in a frame with bolted side panels forming a block shape – GreanBoxTM – Model SP
- Welded Plate Heat Exchangers with Corrugated Plates mounted in a frame and inserted in a shell with a bolted side panel on one side forming a cylindrical shape – Plate and Shell Heat exchanger
GreenBox™ – Model S
The GreenBox™ – Model S is a welded plate heat exchanger, designed with square corrugated plates welded together to form the heat exchanger’s core—known as the “heart.” There are no gaskets between the plates; instead, the sealing is achieved entirely through welding. Only the removable side panels use gaskets for external sealing.
Easy Access for Maintenance
The plate surface area—or heart—can be easily accessed for inspection or cleaning by simply removing the four side panels. This design allows for quick and efficient maintenance without extensive downtime.
Patented Soft Corners for Superior Durability
The patented soft corners design of the heart and panel assembly makes GreenBox one of the most robust and reliable heat exchangers in its class. Thanks to its mechanical strength, it is ideal for challenging process environments involving high pressures and temperatures.
Exceptional Thermal Efficiency
Nexson’s welded plate heat exchangers are built for maximum thermal performance, making them ideal for applications such as heat recovery, interchangers, condensers, reboilers, and evaporators. They also perform well in semi-fouling duties.
High Efficiency vs. Shell & Tube
The corrugated plates in the GreenBox create a highly turbulent flow, making it approximately five times more efficient than traditional shell & tube heat exchangers. With a temperature approach as close as 2°C, GreenBox also offers a compact footprint, reducing installation, operational, and maintenance costs.
Flexible Configurations
GreenBox can operate in single or multi-pass configurations, depending on your needs. Plate access remains simple—just remove the side panels for inspections or cleaning.
Key Advantages
1. Robust and Patented Technology
GreenBox is a patented solution by Nexson, validated through extensive pressure and temperature cycling tests. It sets a new standard in mechanical durability among welded plate heat exchangers.
2. Handles Semi-Fouling Media
GreenBox is engineered to handle one or two semi-fouling fluids simultaneously. Its corrugated plate design ensures high shear stress, minimizing fouling on the surface.
3. Easy to Clean
Maintenance is straightforward—just remove the panels and clean with a high-pressure water jet.
4. Interchangeable Heat Transfer Area
Thanks to its modular construction, the heat transfer area (heart) can be replaced independently from the panels. If your process evolves or raw material requirements change, the GreenBox can be easily adapted, even switching to Nexson’s studded plates for more fouling media.
5. Close Temperature Approach
With high-efficiency corrugated plates and an excellent K-value, GreenBox achieves tight temperature approaches and even crossing temperatures.
6. High Flow Capacity with Low Pressure Drops
This is a multi-section heat exchanger with customizable baffle arrangements based on your flow and pressure drop requirements.
7. Full Access to Heat Transfer Area
Simply remove all four panels to access the entire heat transfer area during scheduled plant maintenance.
Material Selection & Design Limits
GreenBox™ – Models S and W – can be manufactured in virtually any formable and weldable material, including:
Stainless Steels: 304 / 304L, 316 / 316L, 904L
Special Alloys: 254 SMO, C276, Nickel 200/201, Alloy 59
Titanium Grades: Titanium Gr1, Gr11
Other materials available on request
Design Parameters
Design Pressure: From full vacuum up to 50 barg
Design Temperature: From -50°C to 450°C
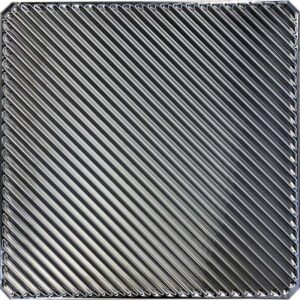
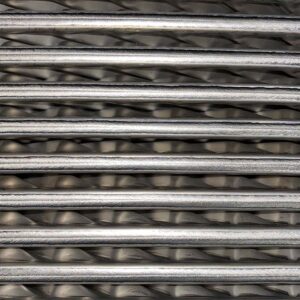
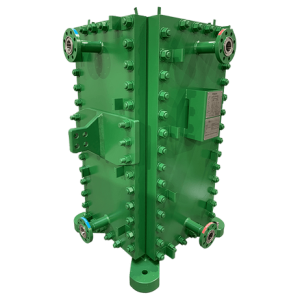
GreenBoxTM – Model W
GreenBoxTM – model W is a variation of the GreenBoxTM – model S but in this case, we have a truly fully welded heat exchanger. As before the heat exchanger is made of square corrugated plates welded together, forming the heart of the heat exchanger. There is no gasket between the plates; the sealing is done by welding. For this model, instead of the removable side panels with gaskets for external sealing, we have 4 semi-shells welded to the plate-pack and closing it completely in a cylindrical shape. As we now have a fully welded and non-openable construction this model is perfect for clean media at high temperatures and/or pressures. As the GreenBoxTM – model W is fully welded no gaskets are needed nor bolts for closing panels at specific torques. This, in combination with Nexson’s patented and robust corner construction, ensures that leakage problems are next to nonexistent, even for applications with periodical operation.
Other than that, the Applications (below), Advantages, Material Selection and Design Limits (above) for the GreenBoxTM – model W are similar to the GreenBoxTM – model S.
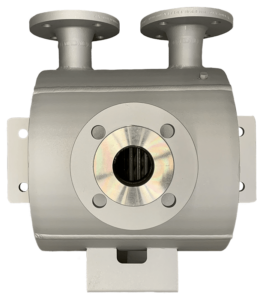
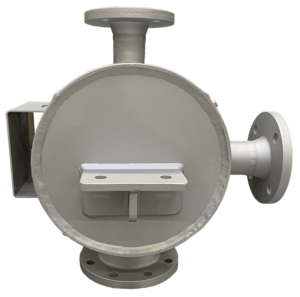
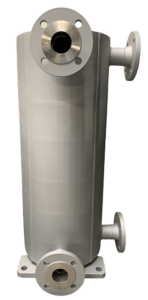
GreenBox™ – Model SP
The GreenBox™ – Model SP is a variation of the GreenBox™ – Model S, developed to overcome limitations related to small channel spacing in traditional welded plate heat exchangers with corrugated plates. These limitations become especially apparent when dealing with fouling media.
Patented Design with Flat Studded Plates
To address this challenge, Nexson has developed a patented solution using flat studded plates, similar in concept to those used in spiral heat exchangers. These plates are welded together to form the core (or “heart”) of the exchanger—just like in the corrugated plate models.
With this design, the stud length and channel spacing can be individually configured for each media side. This allows greater design flexibility, especially when hot and cold sides have different flow rates. Additionally, the larger channel spacing is ideal for applications involving fouling or viscous media.
Easy Access for Inspection and Cleaning
As with the Model S, the plate pack in Model SP is installed within a frame featuring four removable side panels. Removing these panels allows for full inspection of the heat transfer area and enables mechanical cleaning using a hydro jet.
More Robust Construction for Harsh Applications
Unlike corrugated plates, flat plates do not need to be molded, which removes limitations in material selection. The plate thickness is typically greater in Model SP, making it more robust and suitable for erosive media.
Furthermore, flat plates enable the use of less formable, high-performance materials such as Duplex and Super Duplex steels, which offer exceptional corrosion resistance—making Model SP a superior choice for aggressive process environments.
Shared Benefits and Applications
In addition to its unique construction, the applications and advantages of GreenBox™ – Model SP are largely similar to those of Model S, including:
High thermal efficiency
Semi-fouling media compatibility
Easy maintenance
Close temperature approach
High flow with low pressure drops
Modular, interchangeable heat transfer area
Material Selection & Design Limits
The GreenBox™ – Model SP can be manufactured in a wide range of weldable materials suitable for studded plate construction, including:
Stainless Steels: 304 / 304L, 316 / 316L, 904L
Special Alloys: 254 SMO, C276, Nickel 200/201, Alloy 59
Titanium Grades: Titanium Gr1, Gr11
Duplex & Super Duplex Steels
Carbon Steel: SA 516 Gr 60/70
Other materials upon request
Design Parameters
Design Pressure: From full vacuum up to 50 barg
Design Temperature: From -50°C to 450°C
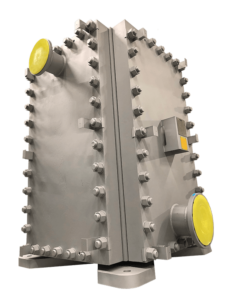
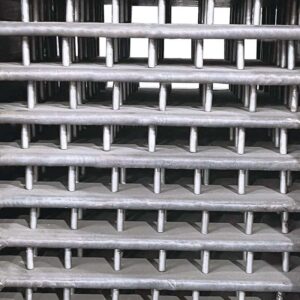
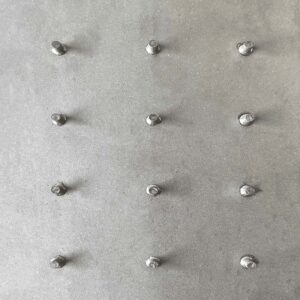
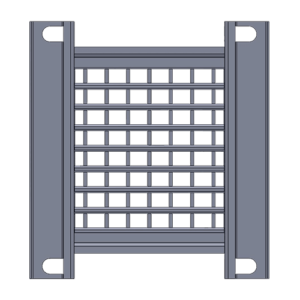
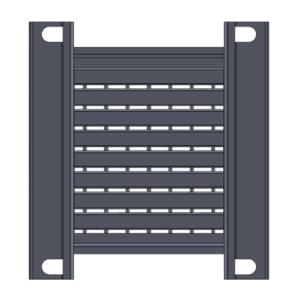
Plate & Shell Heat Exchangers
Nexson Group also offers Plate & Shell Heat Exchangers, where corrugated welded plate packs are inserted into cylindrical shells with an openable panel on one side. The plate pack can be:
Welded into place, or
Inserted with gaskets, allowing for removable construction.
In the gasketed version, the plate pack is removable for mechanical cleaning or even replacement, offering flexibility in maintenance and process changes.
Applications for Welded Plate Heat Exchangers
Liquid-to-Liquid Applications
Welded Plate Heat Exchangers are widely used for liquid-to-liquid duties in numerous industries, including:
Pulp and Paper
Refineries
Petrochemicals
Oil & Gas
Food Industry
Mining
Steel and Metal Manufacturing
Typical applications:
Heat Recovery
Heating
Cooling
Bi-Phasic Applications
Condensation with Sub-Cooling
After condensation, a dedicated section of the heat exchanger can be used for sub-cooling the condensate before it exits the unit, enabled by baffle arrangements.
Evaporation / Reboiler
GreenBox welded plate heat exchangers can be used as thermosyphon reboilers or evaporators, typically operated in single-pass configuration.
Traditional Uses in Bi-Phasic Systems
Used across all major industries (Pulp & Paper, Refineries, Petrochemicals, Oil & Gas, Food, Mining, etc.), welded plate heat exchangers handle phase changes effectively while maintaining compact form and high efficiency.
Welded Plate Heat Exchangers in Industry
These heat exchangers are chosen for their efficiency, flexibility, and robustness. They handle a variety of liquids, semi-fouling or viscous media, gases, and two-phase flows with ease.
Typical uses include:
Economizers
Heaters / Coolers
Condensers
Evaporators
Steam Heaters
Reboilers
Industry-Specific Applications
Oil & Gas Industry
In both onshore and offshore applications, Welded Plate Heat Exchangers often replace traditional Shell & Tube or Gasketed Plate Heat Exchangers, providing more compact and efficient solutions.
Petroleum Refineries
Refineries require heat exchangers for multiple critical processes:
Desalting
Atmospheric and Vacuum Distillation
Catalytic Cracking
Reforming
Blending
There is also increasing focus on biofuel integration and fossil-free feedstocks, with welded plate heat exchangers playing a central role in energy-efficient upgrades.
Petrochemical Industries
These exchangers support the production of a wide array of consumer and industrial chemicals, such as:
PVC and Vinyl Chloride
Polyethylene, Polyamides
Ethylene Glycol, Polyesters
Polystyrene, PET
TDI (Toluene Diisocyanate), MDI (Methylene Diphenyl Diisocyanate)
They enable efficient heat transfer in complex and demanding processes.
Mining and Steel Industries
As industries shift towards electrification and low-carbon processes, heat exchangers are needed for:
Battery mineral production
Carbon Capture & Utilization
Direct Reduction of Iron with hydrogen
Efficiency upgrades in traditional coke-based steel production
GreenBox exchangers help meet these modern energy and sustainability requirements.
Chemical Industries
Welded Plate Heat Exchangers are ideal for the production of:
Sulphuric and Phosphoric Acid
Sodium Hydroxide, Ammonia
Chlorine, Hydrochloric Acid
Hydrogen Peroxide, Formic Acid
Inks and Pigments (e.g. Titanium Dioxide)
These processes demand resilient and corrosion-resistant heat exchanger solutions.
Pulp and Paper Industry
This sector benefits from heat exchangers in both traditional and innovative bio-based applications, such as:
Biofuels from tall oil
Methanol and turpentine production
Sulphuric acid from off-gas
Lignin separation from black liquor
Biogas and bio-pellets
Carbon Capture and BioProduct Mills
Modern pulp mills aim for energy self-sufficiency and even negative carbon footprints—a perfect match for efficient welded plate heat exchangers.
Food Industry
Rising global food demand drives the need for efficient processing. Applications include:
Dairy products, milk proteins
Breweries
Fruit juices
Starch and vegetable proteins
Sugar and alcohol production
Edible oils and fats
Soups and sauces
Even wastewater from food production can be treated for biogas generation using heat exchangers for energy recovery.
Why Choose Welded Plate Heat Exchangers?
Compact footprint with high thermal efficiency
Handles high pressures, high temperatures, and corrosive/erosive media
Suitable for semi-fouling and fouling duties (especially with studded plate versions)
Long-term reliability in demanding environments
Ideal for industries where precise temperature control is crucial