Jet Mixers - Eductors
tank mixing systems
Jet Mixers / Eductors are the most reliable and energy-efficient technology for tank mixing systems
Mixing of liquids is one of the most common unit operations in the process industry for several purposes such as: – Improved mass transfer in reactors; – mixing and homogenization of different liquids, sometimes with solids in suspension; – homogenization of temperature gradients in tanks to obtain an even temperature distribution; – Prevention of sedimentation of solids; – Prevention of crystallization, etc. Erivac can provide ideal solutions for all these applications with Koerting Jet Mixers, or Liquid Jet Mixing Nozzles, or Eductors as they are also called. Koerting liquid jet mixers / eductors are the main components of tank mixing systems which can be applied for continuous as well as discontinuous mixing purposes.
The most common technical solution is mechanical agitators or mixers with an impeller on a shaft powered by an electrical motor. These are very good for many applications but they can have some drawbacks in some cases, for example: – high maintenance costs for rotative equipment and electrical motor; – potential tank leakage along the mixer shaft when installed through the tank wall; – difficult access for maintenance on electrical motor; – eventual necessity for vortex inhibitors in the tank resulting in higher installation cost; – high operational cost due to higher power consumption. Most of those drawbacks can be solved with good engineering for customized installation of Jet Mixers / Eductors with technical support from Erivac and Koerting. Koerting Jet Mixers can be used as complete replacements for mechanical agitators and, in many cases, they surpass their mixing results.
Table of Contents
Working principle
A liquid flow is taken from the tank and supplied to the liquid jet mixers via a centrifugal pump. Inside the motive nozzle pressure energy is converted into kinetic energy. Negative pressure is generated at the motive nozzle outlet and the ambient liquid is sucked in.
The suction flow is strongly intermixed with the motive flow in the adjoining mixing section and accelerated by impulse exchange. The drag effect of the exiting mixed flow increases the mixing effect significantly.
Operation
Jet Mixers consist of a motive nozzle and a mixing section. The liquid motive medium introduced under pressure via the motive connection is usually taken from the tank and delivered into the liquid jet mixers employing a pump mounted outside of the tank. In the motive nozzle the static pressure of the motive medium is converted into velocity generating a corresponding negative pressure at the suction openings, the Venturi effect, which is utilized to draw in the so-called suction flow.
Suction and motive flow are intermixed intensively in this turbulent region at the motive nozzle outlet and in the adjoining mixing section and are subsequently supplied into the tank as mixed flow. The volume ratio between suction and motive flow is about 3:1. The mixed flow exits the jet mixers with relatively high velocity and encounters the liquid contained in the tank, which is subsequently entrained as a result of the mixed flow’s drag effect. Finally, the sum of motive flow, suction flow and drag flow keeps the liquid inside the tank moving. The volume ratio between entrainment and motive flow is between 12 – 80. That is, with 1 m3/h pumped up to 80 m3/h are moved and intermixed.
Customized Solutions
Erivac and Koerting aim to design customized tank mixing system solutions for each specific tank. The purpose of the tank mixing system is to generate a liquid circulation of the whole liquid volume which leads to complete mixing and prevents sedimentation. A guided directional flow will be generated by the jet mixers of the mixing system. Therefore, flow velocities occur, which are higher than the sinking velocities of the particles in the liquid, so that settlement is avoided. The two examples in the figures below illustrate the principle of tank mixing systems.
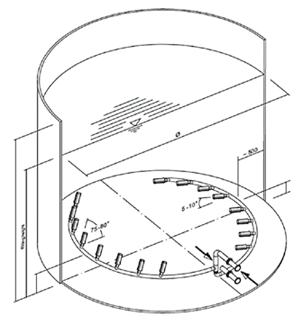
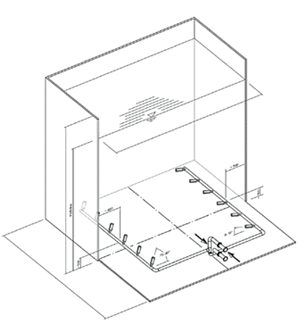
With the options of choosing different jet mixer sizes, adjusting jet mixer rows according to the tank shape, modification of the jet mixer distances and being flexible concerning the operation of the different jet mixer rows Koerting can dimension the optimum tailor-made tank mixing solution for every specific purpose. E.g. for full homogenization, for prevention of settlements, for prevention from different temperature layers, or for a complete mixture of different liquids.
Case Study for Jet Mixers / Eductors in an edible oils tank
The images below give a good impression of a complete tank mixing system with jet mixers in a storage tank for edible oil. 17 jet mixers made of stainless steel are installed nearly horizontally whereas 17 mixing nozzles are installed nearly vertically at the opposite side of the tank. The tank volume is 11 000 m³ with a filling height of 25 m and a diameter of 24 m.
Technical data:
- cylindrical storage tank for edible oil
- 34 jet mixers of stainless steel 2“
- volume 11 000 m3
- height 25 m
- diameter 24 m
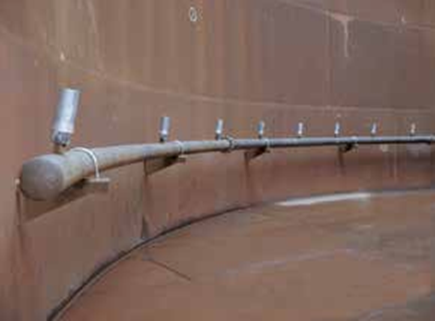
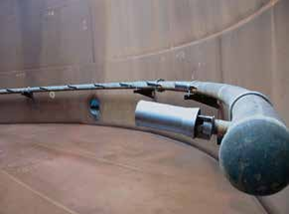
Alignment of the mixing system:
The result of the Koerting design is a sketch for the customer, which contains recommendations and information, so that the mixing system will be installed in the tank in an optimum way. To evaluate critical cases Koerting uses CFD simulation (“Computational Fluid Dynamics”).
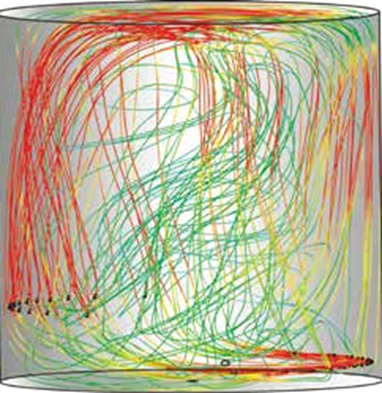
Case Study for Energy Cost Savings
The following example shows the potential of energy savings if applying a Körting tank mixing system:
Tank Dimensions:
Tank Diameter 27 m
Filling Height 10 m
Filling Volume 5 983 m3
Energy Consumption
Mixing with mechanical mixers ~10 W/m3
Mixing with Koerting Jet Mixers ~4 W/m3
Energy saving potential ~6 W/m3
Calculation of Cost Savings
6 W/m3 * 5 983 m3 = 35,9 kW
35,9 kW * 8760 h 314 484 kW/year
314 484 kW/year x 0,2 $/kW 62 897 $/year
Additional savings when sedimentation of main product occurs
In many cases, installed mixing power in tanks is not sufficient, or the velocity and turbulence of installed mixing technology are not applied correctly, which might lead to sedimentation even though this should be avoided. This is often the case in, for example, in Edible Oils, Mineral Oils and BioFuels storage tanks, etc. After some time, the sedimentation will accumulate a considerable layer of sludge with valuable main product on the bottom of the tank. The cost to empty that tank and clean the sludge out is high and requires hazardous jobs in confined spaces that can be avoided. Below is an example of edible oils:
Degummed soybean oil:
Problem: Degummed vegetable oils need quite intense mixing to avoid settlement of gum, with 10% – 30% of the main product edible oil, as a sludge on the bottom of the storage tanks. Conventional mixing with through-the-wall mechanical mixers does not provide the necessary mixing power nor mixing velocities along the tank floor to avoid such settlement.
After 6 months to one year this sludge layer can be up to 1 m high, even with conventional through-the-wall mixers installed.
Considering an example tank with 27m of diameter, as above, a one-meter sludge layer and 20% of oil in the sludge we would have approximately 572 m³ of sludge and a loss of approximately 114 m³ of degummed oil, or approximately 100 ton/year lost. Degummed soybean oil cost approximately US$ 900,00 per ton, thus the raw material loss per year would be approximately US$ 100.000 a year, for one tank only. Apart from the raw material loss these tanks need to be cleaned at least once a year when using conventional mixing technologies, with maintenance in confined spaces that is costly.
In the case above using Erivac support, Koeting Jet Mixers and Experience in an appropriate installation the combined savings, energy and avoiding main product loss, can be as high as approximately $ 160 000 / year for one tank only. The installation cost for a pumps, piping and Koerting Jet Mixers will have a very short payback time. Availability for the tank will be higher as stops for cleaning the tank will be avoided and the cost for this cleaning can also be included in the savings using Jet Mixers.