Waste Water Aeration
Jet Aerators
High efficiency and reliable operation with lower power consumption.
Highly polluted organic wastewater (or with high organic load) requires a lot of oxygen to oxidize and degrade to meet environmental legislation. Thus, modern plants of biological wastewater treatment are constantly looking to increase the height of their tanks in order to optimize oxygen transfer efficiency to the Wastewater. Conventional technologies have proven ineffective for certain applications, such as basin depths greater than 6 meters; high need for oxygen; and high concentrations of sludge and solids. The solution in Europe, with high-efficiency oxygen transfer and a significant reduction of energy consumption, has been the use of jet aerators. With the recent increase in the price of energy and electricity, jet aerators and jet aeration are beginning to gain new users in a variety of industries as well as for sanitary wastewater. Koerting Jet Aerators can be applied in any type of wastewater aeration technology, whether it is Conventional Activated Sludge (CAS), Sequential Batch Reactor (SBR), Membrane Bio Reactor (MBR), or Moving Bed Bio Reactor (MBBR).
Koerting has developed, for more than 150 years, customized solutions of ejectors and vacuum systems for various industries. Over the past 30 years, Koerting has developed a new business segment: Water Treatment and Wastewater aeration with jet aerators. This “new” application for jet aerators was developed with a partner, a well-known German company, especially for MBR wastewater treatment solutions. This company had specific needs to transfer oxygen more efficiently and sustainably in wastewater with high organic loads. The development of this bold solution has, to present date, resulted in over 1200 supplies of wastewater aeration systems.
Ejectors are used in many operations for the treatment of water and wastewater, such as jet aeration and nitrification with jet aerators while jet mixers are used for equalization, homogenization, denitrification, neutralization, mixing, conveying resins, among others. Its design is determined by the types of the motive and suction fluids, as well as the prevailing pressures in the three ejector connections. The ejectors are self-priming, free of moving parts and their mode of operation is based solely on the laws of fluid dynamics. Numerous layout possibilities and layout of ejectors and their different methods of operation, with atmospheric air intake or air from blowers, provide ideal conditions for applications in water treatment plants and wastewater, large and small.
How does a jet aerator function?
The motive fluid passes through the jet aerator cross-section, as shown in the figure below. Along this channel, the cross-section changes area so that the pressure in the nozzle decreases and the driving speed increases (the Bernoulli principle). The motive nozzle was developed especially to promote acceleration and better conditioning of the motive fluid to admit the air/gas sucked through the suction section. The restriction in its spiral increases the shear stress of the motive fluid, promoting grooves and rotation of the jet, making it easier to spray and, by the Venturi effect, the integration with the suction fluid. In this way, it causes a great mix of fluids with high gas saturation of the liquid.
The region with the lowest static pressure is found immediately after the motive nozzle, where suction takes place. Thus, the suction fluid is added and mixed with the motive fluid, further transferring kinetic energy to the suction fluid, and accelerating it. Along the diffuser flow velocity decreases again, causing a pressure increase until reaching the discharge pressure of the jet aerator. The transfer of oxygen depends not only on the size of the bubble (contact surface between the gas and water), but also on the renewal of the contact surfaces of the gas bubbles. This renewal takes place by constant recirculation of the wastewater delivered to the jet aerator by a centrifugal pump.
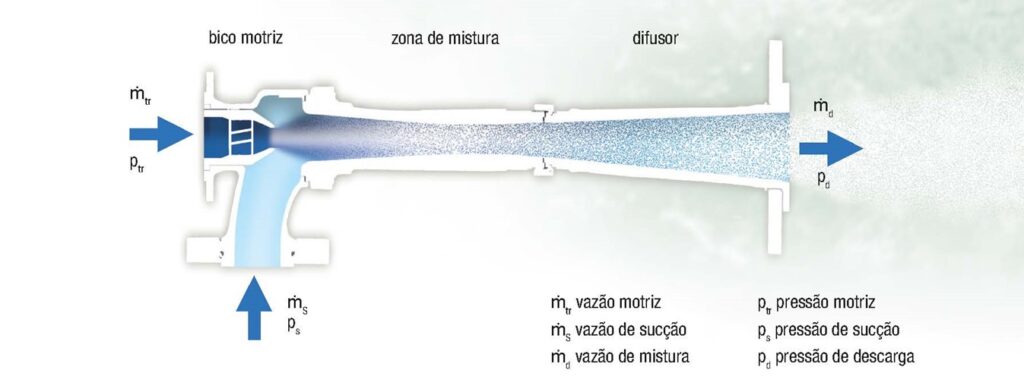
The motive fluid in wastewater treatment applications is normally the recirculated wastewater by centrifugal pumps. The suction fluid, usually air, may be delivered by a blower/compressor or even be drawn directly from the environment by the jet aerator in some cases.
Jet aerators – with the constant mixing of wastewater – can achieve a much higher efficiency than other oxygen aerators. Upon exiting the ejector nozzle, the highly saturated fluid with air bubbles remains as a jet to the tank bottom (50 – 60 cm) and gently contemplates the total height of the liquid level, microbubbles in their coalescing surface. With their flow directions aimed at the tank bottom, the Koerting jet aerators fully utilize the depth of each tank.
Oxygen transfer efficiency and energy consumption
Long oxygen supply tests in pure water (ATV M-209) according to the adsorption method, from the database to the design of the Koerting jet aerators. All measurements were performed on actual plant inspection and confirmed in numerous tests. The efficiency of this operation results in an oxygen absorption rate of the Wastewater up to 3 kgO2 / kWh consumed with alpha x beta efficiency factors of 0.8 – standard value in the design of Koerting jet aerators.
Such efficiency also contributes to a rapid return on investment due to the reduction in the power consumption (power on the axles of the pump and blower) up to 55% or in some cases even greater reduction in comparison with the diffuser systems due to more efficient fine bubbles oxygen transfer and constant surface renewal. It is noted that usually, a reduction in energy consumption increases with increasing depth of the tank.
The control of oxygen inclusion is obtained simply by changing the volume of air integration. A reduced supply of air results in a less intensive regimen of work by the blower/compressor, which works with a lower discharge pressure, thus reducing energy consumption in the operation.
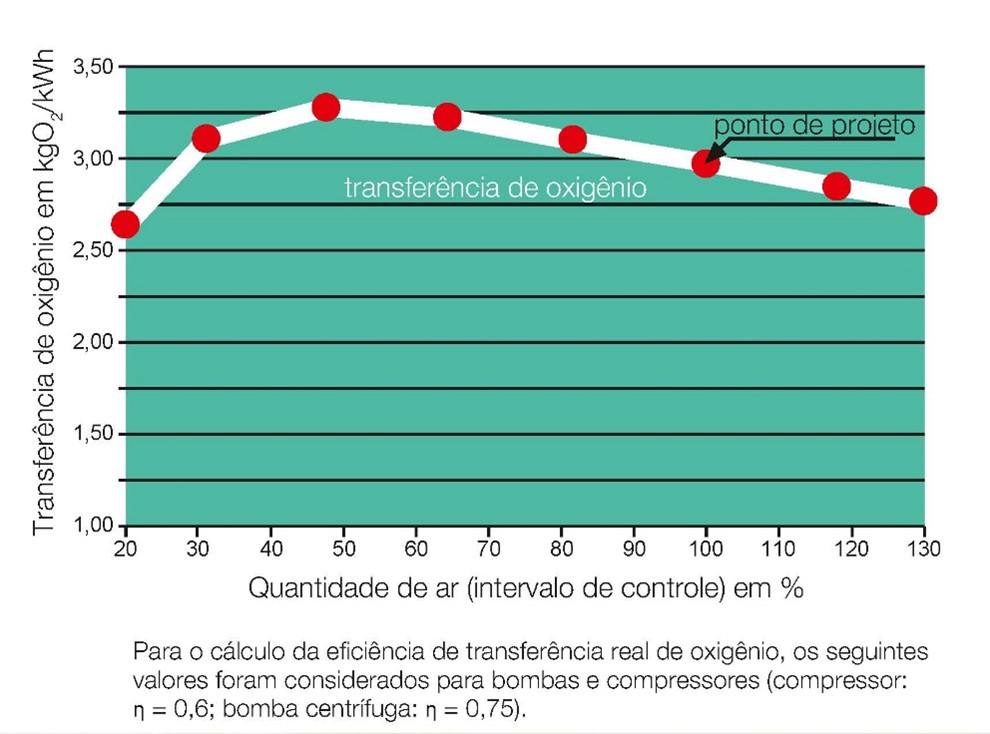
The direction and position of the jet aerators outlet influence the area covered, where the microbubbles will have a slightly longer route to coalesce fully and effectively. Due to the motive flow and turbulence of operation, the pressure drop for the jet aeration system is reduced. In other technologies exists a high resistance for air bubbles to traverse its path, as well as the “fouling” factor which refers to the additional resistance caused by fouling of the air pipe, gradual clogging of the air distribution surfaces of the solid particles and oil from the blower, as well as sludge deposition and microbial growth on this same surfaces. These factors result in higher pressure loss for conventional technologies, requiring higher blower discharge pressure and consequently higher power consumption.
Jet Aerators are designed to not require any maintenance for the first 15 years of use.
Besides the main advantage of a significant reduction in energy consumption, there are noted other factors that make the Koerting jet aerators even more competitive compared to other technologies.
By equipping a tank or aeration pond with Koerting jet aerators, there is no need for maintenance inside the tank, because the ejectors have no moving or rotating parts that may wear with the operation and need repairs. The lifespan of jet aerators in tanks, proven in numerous installations around the world, is more than 15 years and in some cases over 25 years. Conventional technologies, such as membrane diffusers, normally have needs for exchange of the aeration elements every 2-5 years with spare parts cost and considerable time and effort for maintenance.
The maintenance of jet aeration systems over the years of operation will be conducted in the blowers/compressors and recirculation pumps, commonly installed outside the tank to facilitate this maintenance. Thus, it discards the need for emptying of tanks.
Comparative examples – Case Studies
We already have facilities with 25 years of operation without the need for change of jet aerators, even in difficult wastewater applications such as for leachate, diary industry or pulp and paper, etc., and virtually unchanged oxygen transfer from the beginning of the operation.
Below are some examples of energy consumption studies
Wastewater treatment in a rectangular tank with high biomass concentration:
Tank area (m²) | 21 x 5.3 |
Tank depth (m) | 3.0 |
Tank Volume (m³) | 339 |
Oxygen Demand – AOR (kg O2 / h) | 210 |
Biomass Concentration (g / l) | 12 |
This example shows a significant reduction in energy consumption, even with this liquid level height much lower than the ideal. This high efficiency is due to the optimum motive flow mixture thus facilitating contact promoted by Wastewater – air interface within the jet aerators.
Technology |
Jet Aerators |
Diffusers |
Amount of |
3 aeration manifolds with 16 ejectors each |
252 diffusers |
Factor α (alpha) considered |
0.8 |
|
Necessary air volume (Nm³ / h) |
1700 |
5200 |
Energy consumption |
|
|
Recirculation pumps (kWh) |
25 |
AT |
Blower (kWh) |
11.6 |
74.4 |
Total Energy Consumption |
48.2 |
74.4 |
Reduction of consumption (kWh /%) |
26.2 / 35.2% |
|
Total cost of the investment |
$ 112 515,00 |
$ 101 075,00 |
* including pumps and blowers |
||
Operating Cost Reduction |
8760 h / year |
|
Electricity ($ 0.2 / kWh) |
$ 45 902,00 |
|
Wastewater treatment in circular tank with high biomass concentration
Tank area (m²) | 572 (Ø 27m) |
Tank depth (m) | 7.0 |
Tank Volume (m³) | 4,000 |
Oxygen Demand – AOR (kg O2 / h) | 202 – 213 |
Biomass Concentration (g / l) | 8 – 10 |
In this example with ideal depth for use of Koerting technology with considerably larger Wastewater flow rate and tank volume than the previous examples, there is a 55% reduction in energy consumption for the Koerting system with blower compared to competing technology. The reduction of energy consumption and operating costs in this very interesting project.
Technology | Jet Aerators | Diffusers |
Factor α (alpha) considered | 0.8 | 0.55 |
Necessary air volume (Nm³ / h) | 3625 | 8216 |
Energy consumption |
|
|
Recirculation pumps (kWh / day) | 147 | AT |
Blower (kWh / day) | 329 | |
Reduction of consumption (kWh /%) | 182/55 | Reference |
Operating Cost Reduction | 8760 h / year |
|
Electricity ($ 0.20 / kWh) | $ 318 864,00 |
Conclusion
The Koerting continues its heritage of creating innovative and customized solutions with the best possible results in performance and reduction of energy consumption, with robust and durable equipment. Since the creation of ejectors, diverse areas of application in industrial processes have been developed and environmental technology, including the aeration of Wastewater with jet aerators, integrates all these applications in several segments within their processes.
As shown in the above cases, the Koerting aeration technology presented itself economically and with the potential for significantly reduced energy consumption and cost for the unit as a whole (with CAPEX close to the main technologies used in the market, and with OPEX and maintenance costs much lower than these).
The expertise of Erivac and Koerting in this segment is not restricted to the ejector technology, but the complete design of the system as a whole, optimizing equipment design, equipment positions and angles of attack, reduction of pressure drop, development of special nozzles for complex applications.
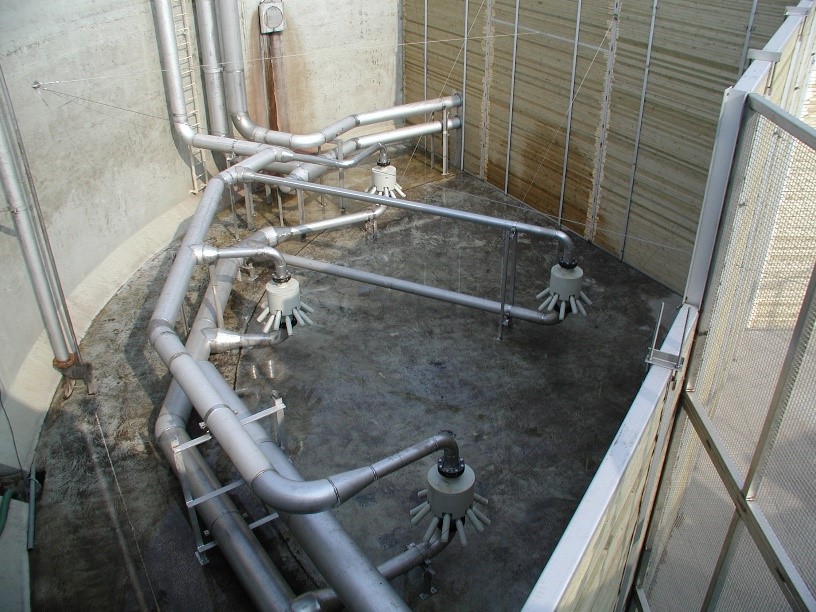
There are plenty of opportunities for use of this technology for any aeration basin or technology, weather it is for CAS, SBR, MBR or MBBR technology path. We can apply our portfolio in various industrial and municipal segments, as well as a variety of custom options for specific types of Wastewaters.
In addition to the aeration system, Koerting also has equally beneficial solutions in terms of CAPEX and OPEX for equalization tanks, anaerobic reactors, ozone insertion in the treatment of drinking water and dissolved air flotation.